VIP member
Ethernet to CAN gateway
● Remote monitoring of CAN bus data ● Connect CAN bus to Ethernet ● TCP to CAN data gateway, converter ● Industrial field CAN bus monitoring ● Protoco
Product details
Equipment Description:The GCAN-212 device from Guangcheng Technology is a module that converts Ethernet to CAN,It can integrate the CAN bus into the existing Ethernet topology, making it suitable for remote monitoring of CAN bus data/status. You only need to connect the Ethernet to CAN module to the local area network, and you can monitor the CAN bus status through the upper computer software at any location that can be connected to the local area network. This module has been widely used in industrial automation systems, railway systems, building automation systems, motor room monitoring, power monitoring and other fields.Consultation hotline: 157 1241 1229





The GCAN-212 series are all industrial grade products that can operate normally within a temperature range of -40 ℃ to 85 ℃. It integrates a 10M/100M adaptive Ethernet interface internally, with multiple working modes such as TCP Server, TCP Client, UDP, etc. It supports Ethernet redundancy and CAN network redundancy. Both CAN and Ethernet interfaces are industrial grade designs, and the CAN interface comes with a magnetic coupling isolation module to avoid damage to equipment due to transient high voltage. Its strong anti-static and surge resistance capabilities make it suitable for use in harsh environments.

Configurable working mode, working port, target IP, and target port.
Supports TCP client mode, TCP server mode UDP。
The supported protocols include Ethernet, ARP, IP, ICMP, UDP, DHCP, DNS, and TCP.
Compatible with SOCKET working modes (TCP Server, TCP Client, UDP, etc.), the upper computer communication software is written in accordance with standard SOCKET rules.
Integrated with 2 CAN interfaces and terminal wiring design.
The CAN protocol fully complies with the CAN 2.0B specification, is compatible with CAN 2.0A, and conforms to ISO 11898-1/2.
The CAN baud rate can be programmed and set arbitrarily, ranging from 5Kbps to 1Mbps.
Secondary development can support various development environments, such as VC, C #, Labview, LINUX, etc.
The electrical isolation between CAN 1 and CAN 2 and the power supply is 1500V, and the maximum ESD protection is 2kV (in accordance with IEC 60601-1).
Temperature range -40~85 ℃.


In TCP Server mode, GCAN-212 does not actively connect with other devices. It always waits for a connection from the TCP client and can perform bidirectional data communication after establishing a TCP connection with the client.

In TCP Client mode, GCAN-212 will actively connect to a pre-set TCP server. If the connection is unsuccessful, the client will continuously attempt to establish a connection with the TCP server based on the set connection conditions. After establishing a TCP connection with the TCP server, bidirectional data communication can be carried out.

UDP mode uses the UDP protocol for data communication. UDP is a non connection based communication method that cannot guarantee the correct reception of data packets sent to the target host. Therefore, in situations where high reliability is required, upper layer communication protocols are needed to ensure data correctness; However, because UDP is a relatively simple communication method, it does not add too much additional traffic and can provide higher communication speeds than TCP to ensure the authenticity of data packets. In fact, in a relatively simple network environment where the network communication load is not too high, the UDP working mode is not prone to errors. Devices working in this way have equal status and there are no servers or clients.

CANet-Wifi-Config-V5Introduction to configuration software:
Use the CANet-Wifi-Config-V5 software included in the CD to configure the basic parameters of the GCAN-212 series modules.

There are 6 tool buttons above the software:
Connect "- Connect devices;
Upload "- Read out the configuration information from the device;
DownLoad "- Download configuration information to the device's Flash;
Open "- Open to read the configuration information file from the PC;
Save As "- Save the configuration information file to the computer;
UpData App - Upgrade GCAN-212 firmware kernel. (Please use this function under guidance)
Set IP address

Set the communication address information for CANET in the software 'IP Address Info'. There are three parameters that can be set.
IP Address "- Set the GCAN-212 IP address;
Subnet Mask "- Set GCAN-212 subnet mask;
GateWay "- Set up GCAN-212 gateway.
Set CAN bus information

CAN bus communication information can be set in the software "CAN1/2 Info".
'Tcp Port' - Set the CAN bus communication port;
Can Baud "- Set the baud rate for CAN bus communication;
Can Mode "- Set the CAN bus working mode;
Tcp Mode "- Set TCP working mode;
Remote IP "- Set the target host IP address;
Remote Port "- Set the port number of the target host.
Note: "Remote IP" and "Remote Port" are only valid in TCP Client mode and UDP mode.
Introduction to CANET Routine Testing Software:
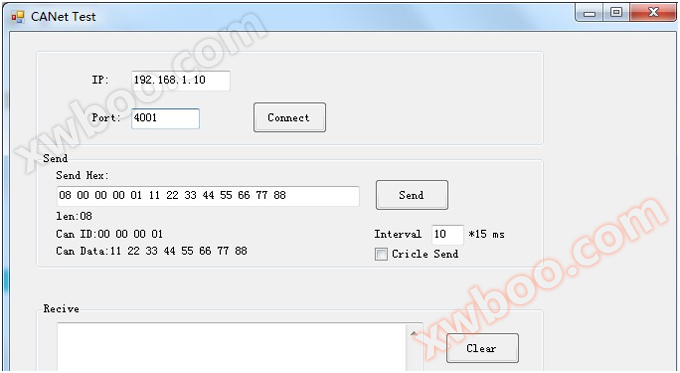
Our company provides GCAN-212 routine testing software for users to test whether the basic functions of Ethernet and CAN terminals are normal. Enter the CANET IP address and corresponding CAN port number, click Connect to establish communication, edit the data in Send according to the rules after establishing the connection, and click Send to send data to the CAN bus; When there is data transmission on the CAN bus, CANET will automatically receive it and list it in the recursive window.
This software is based on We provide users with the source code of the routine software developed by NET.
Our company also provides users with a network debugging assistant, which they can use to develop and test socket communication.

The GCAN-212 module supports secondary development, and the Ethernet end conforms to the standard socket server communication method. Users can develop their own upper computer software according to this communication standard specification. For specific Ethernet data flow definitions, please refer to the "GCAN-212 User Manual".

Remote monitoring of CAN bus data.
Connect the CAN bus to Ethernet.
TCP to CAN data gateway, converter.
Industrial site CAN network monitoring.
Automatic protocol conversion to achieve automatic control.
In addition to the general Ethernet CAN module, our company can also provide Modbus CAN module for users who use Modbus TCP/RTU communication protocol. With this module, a Modbus address mapping table can be configured, and users can configure CAN bus data transmission and reception Modbus addresses according to their actual needs, making it convenient for users to use.

Online inquiry